它“混迹”于公司大修一览表中,却不是一个检修项目;
它比新建装置的难度大,却比任何一个新建装置用时都短;
它让所有参与其中的生产人员,懂了设计、通了施工……变得很不一样;
它因为肩负的使命,成了本次大修现场广泛关注的焦点……
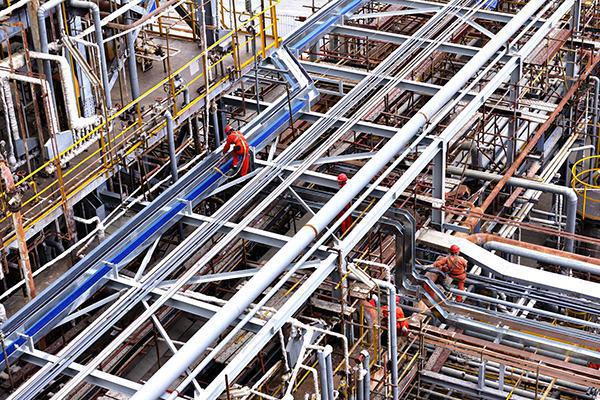
在公司今年大修的重点项目中,有一个项目的工期是最长的——120天。它就是乙烯老区聚乙烯装置催化剂直注技术改造项目。
公司科技信息处刘继新却说:“120天对这个项目来说实在是太短了,因为它不是检修项目,而是老区乙烯装置的改扩建项目,改造比新建的难度更大。”
这个项目从签订技术协议到最终完工开车,计划用时不到1年。这里每天开工最早,收工最晚。
空间局促,先拆后建,点多面广,安装精度高,作业风险大……这些都让直注项目的施工变得非常困难,成了焦点。
标志性一吊
8月6日,重达22吨的种子床料仓开始吊装,这是该项目中最后一个大型设备的吊装。
此次吊装,仅是摆吊车的位置,就花去了半天的时间。因为施工的地方寸土寸金,实在是有点儿小了。
聚合框架高45米,共有7层平台,为了拆除旧设备,一路打通拆除至18米,紧接着又一路安装新设备到45米。平均每层都有多个焊接作业点,现场每天施工人员达230余人。为了确保安全风险受控,现场有作业点的地方都有车间属地监护,同时也有施工方监护。
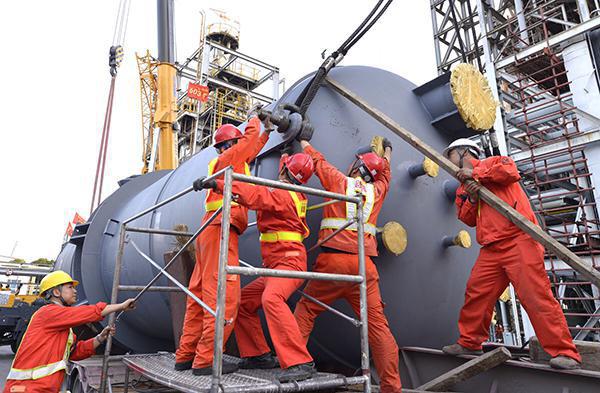
聚烯烃二联合车间工艺生产副主任赵劲操说:“因为空间狭小,300吨的吊车需要将16米高的料仓先高高举起,越过30米高的框架,再下降高度放到预留位置上,难度很大。”
晚上9点25分,经过一个小时的奋战,种子床料仓吊装成功,接下来就是新管线的铺设安装。局促的空间让有些新管线只能钻、绕,这对于现场设计人员、施工人员都是不小的考验。
首次深度介入
直注改造项目是公司首个生产人员深度介入的装置改扩建项目。
聚烯烃二联合车间主任张明建说:“可以说是集全车间之力,深度介入,从设计和土建开始,一直到竣工验收。”
车间人员和设计人员一起设计,和施工人员一起早上6点上班、晚上11点收工,和安全监护人员一起寸步不离监护每一处作业点……
深度介入有利于车间生产人员在将来的生产运行中熟练掌握新工艺的操作原理和方法,为公司生产新产品打下坚实的人才基础。
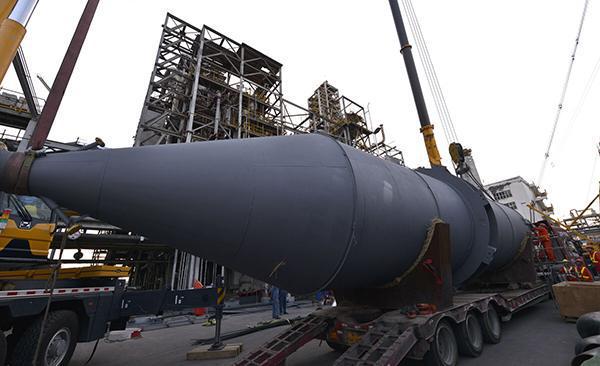
迈向高端化
老区乙烯1993年开工运行至今已有26年。受工艺技术限制,老区聚乙烯21、22线产品结构单一,高附加值产品少,影响装置整体效益及市场竞争力。
为了改善老区聚乙烯装置运行稳定性和安全性,石化公司决定将聚乙烯装置催化剂预聚合工艺改为催化剂直接注入技术。改造后的装置将省去预聚合和催化剂现场制备的环节,可大大提高生产效率,节约运行成本,降低装置能耗,改善产品性能,优化产品结构,可生产更加多元化、高附加值的产品,使聚乙烯产品向差异化和功能化方向发展,进一步提升企业的竞争力。
张明建说:“我们的目标是,确保直注项目和公司大检修同步完成并开工。改造后的老区聚乙烯装置,也将因为更加先进的技术、更低的生产成本而成为公司新产品研发、高端化战略的主战场之一。”
|