废料堆里捡回300万
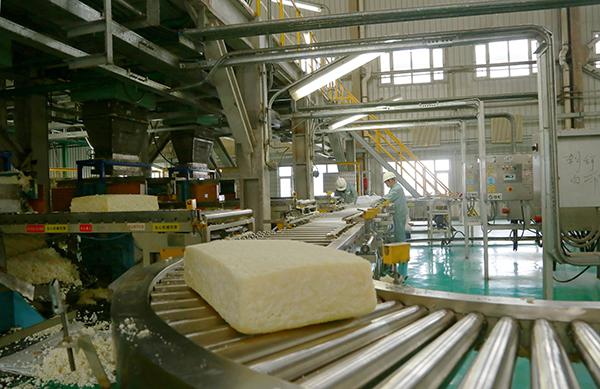
橡胶联合车间丁苯橡胶装置后处理生产线为开放系统,是生产橡胶成品的工段。
正常生产时,在装置现场除了可以看到合格的橡胶压块成品外,还能看到部分水胶、碎料、黏料,也就是曾经员工们眼里的“废胶”。遇到装置定期检修、开停工、设备维护时,该工段产生的废料会更多。据车间统计数据显示,仅丁苯橡胶装置后处理1600、2600两条线,每年就能产生500吨废胶。
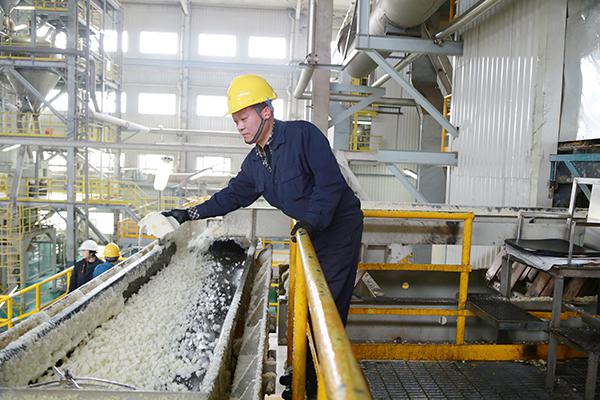
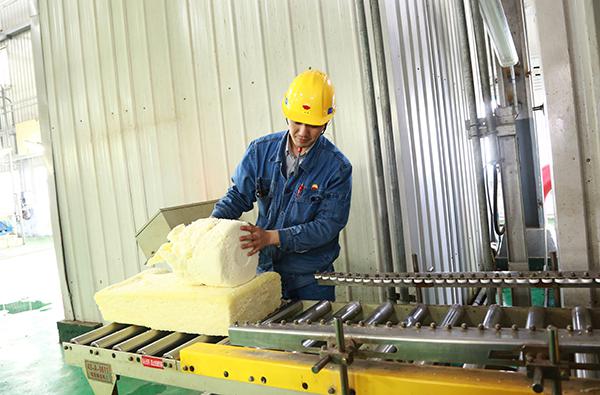
2019年,乙烯厂明确提出了“三期发展目标”,其中,做精生产优化、实现检修前后生产经营业绩超同期最高水平,就是近期目标的主要内容。
如何创收增效?如何保持生产经营业绩?橡胶联合车间立足自身,寻找效益增长点。处理1600线、2600线的废胶,成为车间降本增效的抓手之一。
从今年1月开始,车间对废料的种类、来源进行分析,并制订了具体回收计划及办法。经过论证和实践,回收后的水胶、碎料、黏料等进入生产流水线,就变成了合格产品胶。废胶的销售价为每吨5000元,合格胶的市场价在每吨11000元左右,车间每回收一吨废胶就可增效6000元。
于是,该车间后处理工段的当班员工开始回收废料,他们提着盛满废料的桶、抱着每块为25公斤的成型水胶,往返于相隔几十米远的操作平台和垂直输送机之间。效益有了,但问题也来了。大家发现,靠着小桶盛装、人工搬运,每天只可回收400公斤左右废胶,效率低不说,而且在捡料过程中也存在安全风险。
既要有效益,也要保安全。在工艺副主任杨昌辉的组织下,车间后处理工艺与设备技术员们集思广益,研究出了一套可行的回收办法,即在2600线、3600线操作平台之间增加一条通道,将挑出的水胶和挂壁胶,用小推车经新增通道送至3600线,利用备用压块机压块后,再利用废胶回收单元进行回收。
3月底,连接2600线和3600线操作平台的通道投入运行。如此一来,当班员工的劳动量减少了,也避免了机械伤害的危险。通过新建通道的“过渡”,可以实现后处理1600线、2600线每年产生的500吨废胶全部回收。
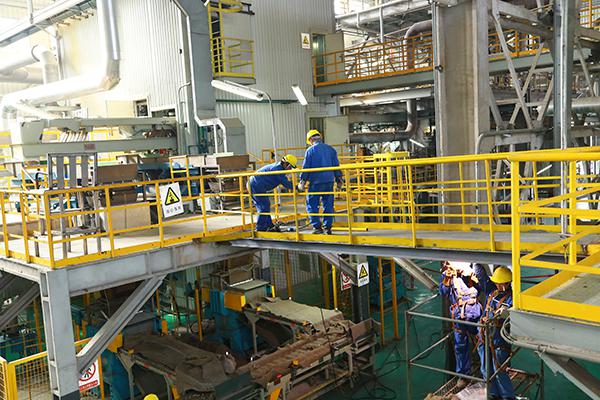
从废料堆里找效益,橡胶联合车间一年预计可“捡回”近300万元。
包装袋里挤出50万
“一条包装袋多装了5公斤,外观好看了,关键是节省了成本。”3月22日,橡胶联合车间丁苯装置后处理工段员工王兴鹏说。
将产品包装规格净含量由15公斤更换为20公斤,年省成本可达50余万元。橡胶联合车间在包装袋上念起了“节约经”,并取得了成效。
在公司及乙烯厂深入实施开源节流、降本增效工程的大背景下,橡胶联合车间各班组员工立足岗位节能降耗,人人参与挖潜增效,助力安全生产管理。
今年1月,该车间丁苯装置3600线生产T162产品,后处理包装线使用的为净含量15公斤的包装袋。员工们在操作过程中发现,因堆积密度与其他产品存在差异,封装完毕的T162包装袋上方空余太多,存在外观不美观和浪费现象。班组向车间提出了“将包装袋净含量由15公斤更换为20公斤”的想法。
经评估核算后,车间对T162产品净含量20公斤包装袋使用情况进行了测试,发现20公斤包装袋完全可以满足生产及包装需求。车间换包装袋的做法,得到了石化公司及乙烯厂相关部门的认可。
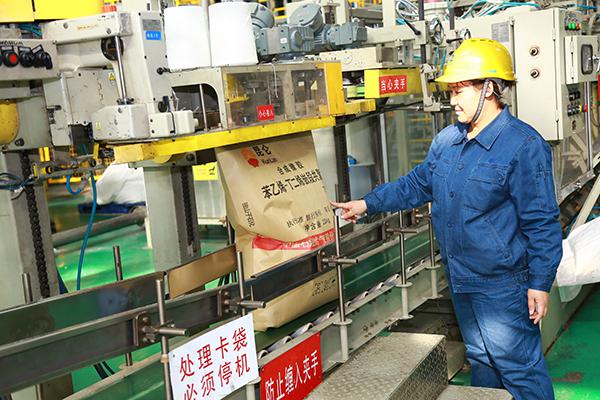
3月15日6:17,在包装袋大小不变的情况下,丁苯装置后处理3600线正式更换新字样的T162产品包装袋。从批量运行的效果来看,达到了优化操作、降低劳动强度、节能降耗的预期目的。“T162产品包装规格净含量由15公斤更换为20公斤”的项目,也被车间列为2019年青工创新创效项目。
班组员工开动脑筋、集思广益,换来的是实实在在的效益。使用新包装袋后,每吨胶使用袋子的数量将从66.6条减少到50条,以每条包装袋4.23元的价格计算,每吨胶的包装成本减少了70.5元。仅这一项,预计每年可节约50多万元成本。
“生产的每个环节、每一名员工,都有可能是企业效益的增长点。结合单位的生产实际,用心多加思考,其实开源节流、降本增效离我们并不遥远。”杨昌辉说。
从点滴入手,省出来的是“真金白银”;靠精打细算,能算出来“金山银山”。公司要实现开源节流、降本增效,需要全体员工进一步强化效益意识、节约意识,立足岗位做好技术创新,精打细算,“锱铢”必争。
|